Creating a DIY battery pack using LFP cells, is a very interesting project for various applications like powering small vehicles, boats, and battery backup for solar power systems. Let’s get into the guide directly.
Here is a concise overview of the key steps for creating a DIY LiFePO4 battery pack: energy sources like wind, hydro and solar power with non-clean energy sources like coal and petroleum.
1. First Planning and designing stage:
First, we need to decide following three key things.
- Analysing the battery capacity:
The very first step of Building a DIY LiFePO4 battery pack, is to determine the key requirements for the application. Deciding on the total capacity (in kWh) that you need is the very first step. That is what battery pack is used for, storing the energy.
- Voltage of the battery pack:
Next, you need to choose the appropriate system voltage for your project. Common options include 12V, 24V, 48V, and 96V. The advantage with higher the voltage is, for the same wattage you get lower amperage in the system. Lower amperage allows the use of thinner wires, reducing the cost of the wires used in the battery system. This not only reduce the cost but also improves efficiency with lower energy loss due to low resistance.
So by opting for a higher voltage, you can improve the system overall efficiency and save money on the wires. However, this comes with the trade-off of increased shock hazard risk. After deciding voltage of the system, this will then determine how many individual LiFePO4 battery cells you’ll need to connect in series to reach that target voltage level. For example, a 12V (12.8V) pack would require 4 cells wired in series, while a 24V (25.6V) pack would need 8 cells in series.
- Compute Battery pack configuration:
As discussed above we now know how our required capacity and our system voltage. Now we are going to finalize our battery pack cell arrangement.
- Series Connection (S): Connecting cells in series increases the voltage. For a 24V system using 3.2V LFP cells, you need 8 cells in series (8S) because 3.2V * 8 = 25.6V.
- Parallel Connection (P): Connecting cells in parallel increases the capacity. To achieve 460Ah, you might use cells with a capacity of 230Ah each, and thus connect two sets in parallel (2P) to achieve 100Ah (230Ah * 2 = 460Ah).
For my example calculation:
- Voltage: 24V (8 cells in series, 8S)
- Capacity: ≈5kWh (230Ah*25.6V≈5.89 kWh) : 230Ah (1 cell in parallel, 1P)
- Total Cells Needed: 8S1P configuration means 8 * 1 = 8 cells.
2. Select the LiFePO4 Battery Cells
Why LFP batteries over Lithium iron batteries?
As a side note comparing the key advantages of LiFePO4 batteries over other lithium-ion chemistries for DIY battery pack projects:
Advantage | LiFePO4 (LFP) | Li-ion (NCA, NMC) |
---|---|---|
Safety | Inherently safer, less prone to thermal runaway | More prone to thermal runaway issues |
Cycle Life | 2,000-5,000 cycles | 500-1,000 cycles |
Thermal Stability | Maintains performance well up to 140°F | Degrades faster at high temperatures |
Cost | Lower cost per kWh | Higher cost per kWh |
TABLE 01: LiFePO4 (LFP) and Li-ion cell comparison.
By choosing high-quality LiFePO4 cells, you can build a safe, long-lasting DIY battery pack that takes advantage of the inherent benefits of LFP chemistry. The lower cost and enhanced safety make LiFePO4 an excellent choice for DIY projects.
Before buying LFP cells we should consider its spec and price related to specifications. The most important factors are cell capacity, cycle life, and depth-of-discharge (DoD) rating, as these directly impact the usable energy, longevity, and safety. Following table 02 includes the main key features and spec that one should consider when selecting a LFP cell technically.
Specification | Typical Range |
---|---|
Nominal Voltage | 3.2V per cell |
Cell Capacity | 100-300Ah |
Cycle Life | 2,000-5,000 cycles at 80% DoD |
Operating Temperature | Discharge: -20°C to 60°C, Charge: 0°C to 45°C |
Specific Energy | 90-160 Wh/kg |
Charge Time | 1-4 hours, depending on charger |
Table 02: Key specifications to prioritize when selecting a LFP cell.
3. Selecting a BMS according to Voltage and Current Requirements:
Let’s do some simple math to find what is the rating of the BMS needed for this Project:
Let’s say peak wattage we need is 3000W and nominal voltage of our (24V) system is 25.6V.
Highest voltage is 3.7v*8 = 29.6v. And for the peak current,
3000W/25.6V=117.18A
So our project BMS was selected with max current 130A and along with a fuse of 125A DC.
Other than this should look for Essential Features:
- Cell balancing
- Overcharge/discharge protection
- Temperature monitoring
- Communication options (e.g., Bluetooth for monitoring)
4. Assemble the Battery pack
- Connect the Cells together.
- Connect the Cells together.
Before putting battery pack into operation, perform cells top balancing procedure. This involves fully charging all the cells to their maximum voltage (usually around 3.65V for LiFePO4 cells) to ensure that each cell starts at the same voltage level. Top balancing helps to equalize the state of charge among all cells, which is essential for the efficiency of the battery pack.
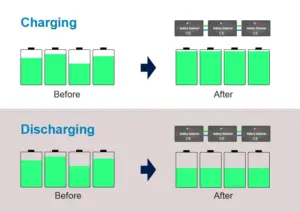
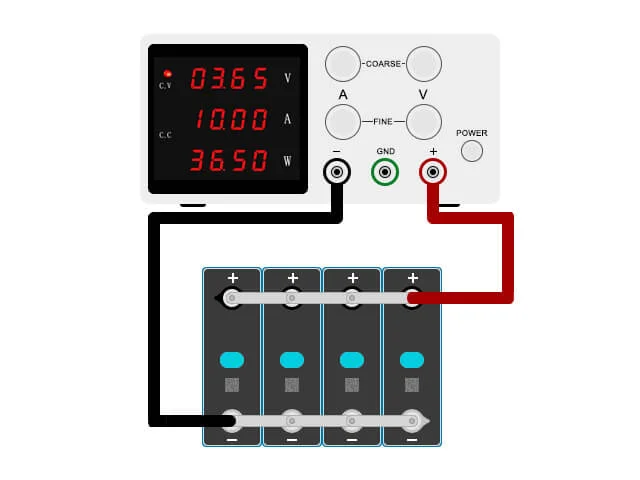
- Connect Battery Cells
For the tutorial 24V system, with 8 cells in series (8S), connect each cell’s positive terminal to the next cell’s negative terminal using bus bars or heavy-gauge wires. Ensure that all connections are secure and well-insulated to prevent short circuits.
- Mount and Connect the BMS
Once the cells are connected, it’s time to integrate the Battery Management System (BMS). Carefully follow the BMS manual to connect it to the cell terminals and the pack outputs. The BMS will manage the charging and discharging of the cells, ensuring they remain balanced and protected against overcharging, over-discharging, and other potential issues.
Use Correct Wires: Selecting the right wires for connecting the cells and the BMS is crucial for the safety and performance of your battery pack. The wire gauge should be appropriate for the maximum continuous and peak currents which is 125A for our tutorial. A wire gauge of 1/0 AWG (35 mm2) was selected for the DC section from the battery cell to the terminal. Additionally, ensure that all wires are well-insulated too as battery terminals and capable of withstanding the environmental conditions.
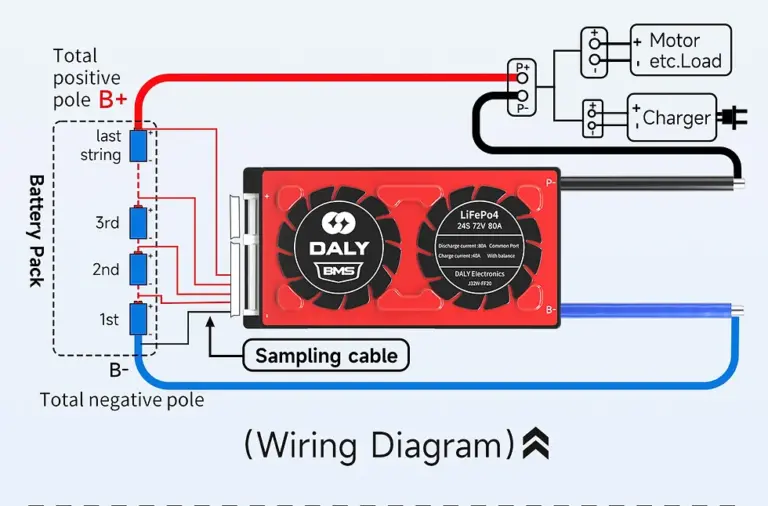
For this tutorial we are using DALY BMS and active balancer separately.
Reference link:
Instruction set for how to install BMS correctly. For this tutorial, we use a 9-string Dally BMS
(link)
- Arrange the Cables: Arrange the 9 strings of cables in a row, with the black cable on the left. Mark the black cable as B0. The first red cable next to the black cable is marked as B1. Continue marking the red cables sequentially: B2, B3, B4, B5, B6, B7, and B8. Ensure all cables are correctly labeled for easy identification and connection to the 8S battery pack.
- Connect to Battery Cells: Now, connect the B0 (black cable) to the negative terminal of the first cell. Connect B1 (first red cable) to the positive terminal of the first cell. Continue connecting each subsequent red cable to the positive terminal of the next cell, up to B8 (last red cable), which connects to the positive terminal of the last cell.
- Integrate with BMS: Refer to your BMS manufacturer’s instructions for specific wiring details. Typically, the B0 cable connects to the B- terminal on the BMS. Connect the remaining cables (B1 to B8) to the corresponding balance leads on the BMS. Connect the BMS P- (or BMS- depending on the model) terminal to the main negative terminal of the battery pack. Connect the main positive terminal of the battery pack to the BMS P+ (or BMS+ depending on the model) terminal.
- Verify Connections: Double-check all connections with a multi-meter from the first pin to incrementally towards the last pin (roughly in 3.6V steps) to ensure they are all connected and ensure that the connections are secure and properly insulated and match the manufacturer’s wiring diagram.
- Power On and Test: Power on the BMS and verify that all cells are properly balanced. Check for correct voltage readings and proper functioning of the BMS.
This Dally BMS came with a separate active balancer, which I installed by connecting it sequentially from the first terminal to the last terminal of the cells.
Additionally, BMS models usually supports Bluetooth or Wi-Fi, you can use those options for monitoring. In this tutorial, we are using the Dally BMS, which supports Bluetooth monitoring. I installed the corresponding app from the Play Store or App Store to facilitate this.
- Build the structure or enclosure for the battery pack.
To finalize the battery pack, start by constructing a sturdy, well-ventilated enclosure for the cells, BMS, and active balancer. Arrange and secure the cells in series (8S configuration), then connect the BMS and active balancer sequentially from the first to the last cell terminal. Attach the main negative terminal to the BMS B- terminal and the main positive terminal to the BMS B+ terminal, add an appropriate (125A for our tutorial) fuse in series with the positive terminal. Ensure all connections are secure and insulated. Power on the BMS, verify proper operation via the app if available, and close the enclosure. This completes the LFP battery pack project.
5. Connect to the load and maintenance
Perform a balanced charging cycle to ensure all cells are equally charged. Monitor the pack closely during the initial charge. Regularly check cell balance and overall pack health. Use the BMS to monitor and maintain the pack over time.
Now LiFePO4 battery pack is ready to power your applications. For me, it was for my off-grid solar project. Enjoy your project and the benefits of your custom-built power solution! If everything goes well, consider buying me a coffee.
You can find the link here.
Feel free to reach out for support anytime via wowsciencefacts social media or directly through the website wowciencefacts.com.